5S
5S is a method to improve and sustain workplace organisation. 5S represents 5 disciplines for maintaining a visual workplace (visual controls and information systems).These are foundational to continual improvement and a manufacturing strategy based on “Lean Manufacturing” (waste removing) concepts.
Need for 5S:
Most employees grow accustomed to “searching” as part of their jobs. They search for parts, carts, tools and information. The more searching they do, the lower their productivity sinks, and the more obsolete their work area becomes. People take little notice of the five minutes they spend searching for jigs, tools, dies, information and carts during an hour-long changeover procedure. But when the factory switches to single changeovers, those five minutes of searching time suddenly become an obvious waste.
The facts are simple:
- A neat and clean workplace will have higher productivity.
- A neat and clean workplace will turn out fewer defective products.
- A neat and workplace will make more on-time deliveries.
5S has lot of benefits for workplace:
5S help reduces clutter, reduces the time it takes to look for tools and equipment. Improves how the operation appears to customers – always be “tour ready”. Creates pride in the workplace. Many companies have a standard that any tool must be able to be found within 60 seconds.
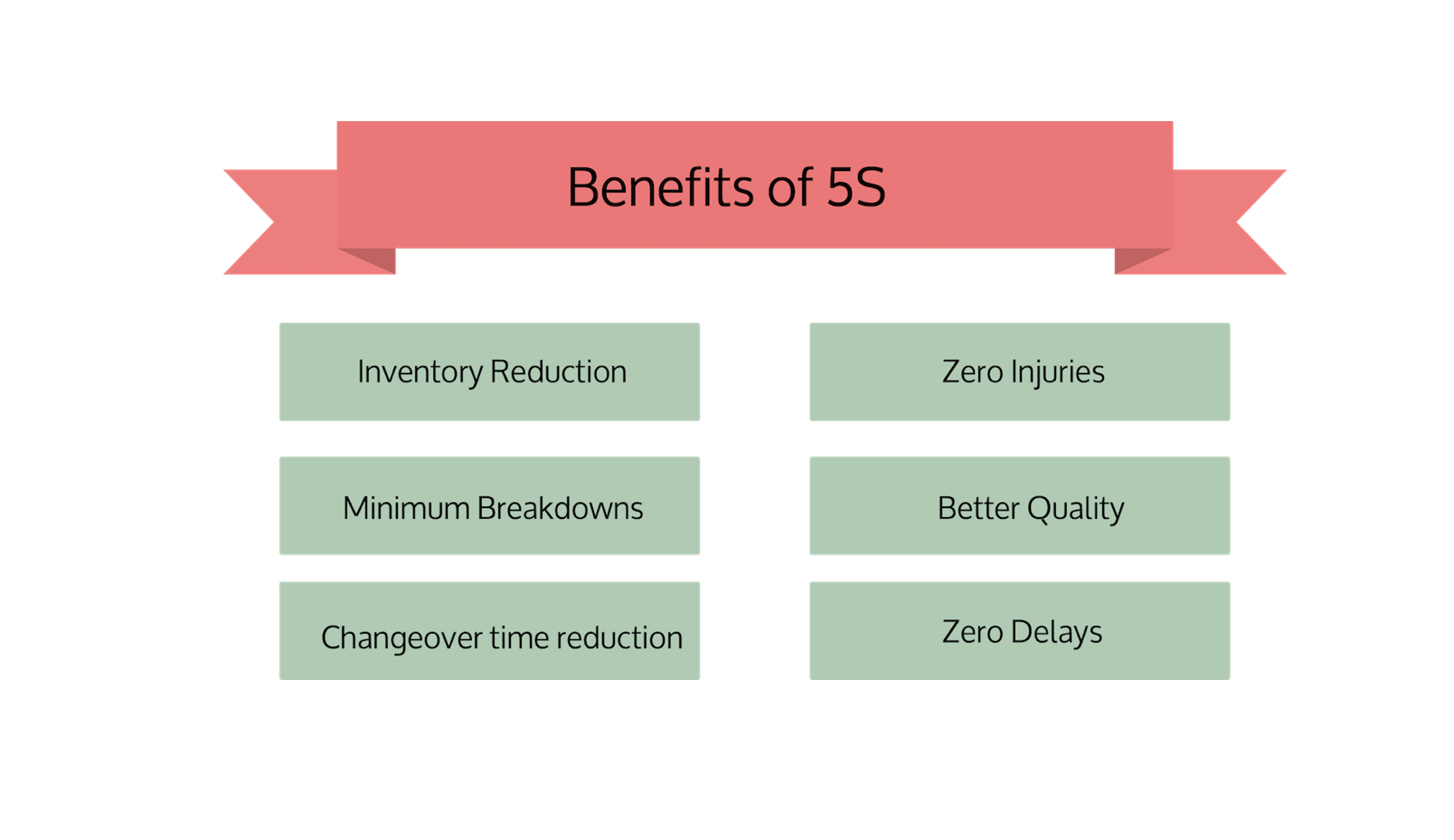
5S are 5 Japanese / English words starting from the word S. In East African Language (Kiswahili) – 5S is known as 5K. 5 Kiswahili words starting from the word K.
1S – Sort / 1K – Kuchagua: Remove all unnecessary materials and equipment
- Unneeded items at workplace contribute to errors and defects.
- Unneeded inventory incurs extra inventory-related expenses.
- Stocked items become obsolete due to design changes, limited shelf life, and so forth.
- Unneeded in-process inventory leads to quality defects
- and machine breakdowns
- Unneeded equipment is a daily hindrance for production activities.
One of the key strategy for 1S implementation is Red Tagging, where Red Tags are attached to unneeded items and unwanted items to moved to Red Tag Area and then decisions are taken to get rid of these items. Red Tags must be attached to items that are completely unneeded, Needed but not now, Needed but not at work area, Needed but is in surplus quantity
2S – Systematic Arrangement / 2K – Kupanga: Make it obvious where things belong. One of the Key principle of Systematic arrangement is Place for Everything and Everything in its Place
Once unnecessary items have been removed from work area next step is is to clarify where these things belong so that anyone can immediately understand where to get them from and where to put them back. In this sense, systematic arrangement means standardizing the places where we keep things.
2S means organizing the way we keep necessary things, making it easier for anyone to find and use them. Key idea is anyone should be able to easily understand the order of things in the workplace.
The signboard strategy is a visible orderliness method that helps anyone understand where things go and thus helps make operations run more smoothly.
3S – Shine / 3K – Kusafisha: Clean everything, inside and out
Cleanliness in a work area is closely related to the ability to turn out quality products & services. Key points in cleaning are to find ways to prevent dirt, dust, and debris from piling up in the work area. Cleanliness should be integrated into everyday tasks.
4S – Standardise / 4K – Kudumisha : Establish policies and procedures to ensure 5S . in 4S, standards are created to ensure effective implementation of Soring, Systematic arrangement & Cleaning For example, Standards are created to keep unwanted away from work area and standards for dealing with Red Tagged items. Standardisation also includes creating standards for labeling, color coding and creating signboards, Cleaning schedules and methodology
5S – Sustain / 5K – Kufundisha : Training, daily activities to sustain 5S
The first four S’s can be implemented thoroughly without major difficulty if the works area is already one where the employees follow 5S standards on a daily basis, regular auditing is to done ensure sustenance of 5S.
Safety (often called “6S” or “5S + 1”) is generally added to 6S to ensure Safety at workplace