Lean Kaizen in Plastic
Make your plastic moulding business 30% more productive and save costs by eliminating waste through lean Kaizen implementation. Before investing in new equipment, generate more productivity from existing machinery or before adding new manpower, increase productivity of existing manpower. With effective implementation of kaizen tools, large organisations in plastic industry have been able to:
Minimise cycle times
Reduce set up times
Reduce rejections and defects
Reduce energy bill
Save plastic material
Reduce machine damages
Our team of consultants have in-depth technical expertise & have successfully implemented Lean Kaizen tools. Our team work closely with client’s employees to transform them into Kaizen experts. Our clients have achieved both qualitative & quantitative benefits with customised Kaizen model of success:
40% increase in output by implementing TPM (Total productive Maintenance)
50% reduction in rejections by implementing Total Quality Management (TQM), Root cause analysis, TPM
50% reduction in inventory by implementing Just-in-time & Kanban
90% elimination of stock outs by implementing Just-in-time & Kanban
Employee Skill improvement by implementing TWI (Training within Industry)
Our Clients in plastic industry
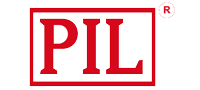
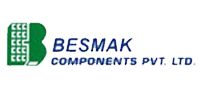
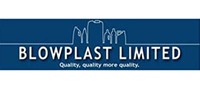
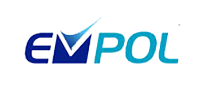
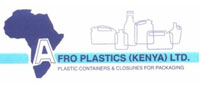
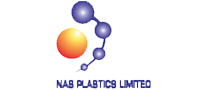
View Productivity improvement journey of India’s leading plastic component manufacturer >
If you are looking to implement Kaizen effectively to deliver great results, we are there to serve you. Kindly get in touch with us at India: +91 9501082279 | UAE: +971 528412755