TPM Consulting Services
Maximise Equipment Effectiveness and Eliminate Losses with TPM
In the evolving landscape of maintenance, the emphasis is shifting from merely resolving breakdowns to predicting and preventing them. To effectively implement a model based on Total Productive Maintenance (TPM) principles, we need to design predictive and planned approaches that will optimize spare parts stock management, reduce equipment downtime, and maximize efficiency.
Total Productive Maintenance or TPM is a comprehensive approach to improve efficiency, productivity and reliability of the equipment throughout its entire lifecycle. To maximise the equipment effectiveness, TPM aims at eliminating 16 Major losses, which obstruct production efficiency.
Our Total Productive Maintenance consulting is directed towards the ultimate goal of zero equipment breakdown and zero product defects, which in turn results in improved utilization of production assets and plant capacity. Our TPM consulting also includes designing and installing equipment that needs little or no maintenance and setting up processes for quickly repairing equipment after breakdowns occur.
With our extensive experience in Total Productive Management consulting for various companies in Kenya and India, we are recognized as one of the leading TPM consultants today. If you are seeking Total Productive Maintenance consultants, please feel free to contact us.
Our Impact
Our Experience
What to Expect?
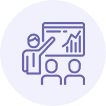
Expertise
Our customized TPM implementation approach focuses on identification of major OEE losses and selecting key TPM pillars to address major losses. Our TPM consultants’ expertise ensures that your teams are well-equipped to maximize the benefits of TPM implementation.
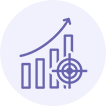
Engagement
Our TPM consultants engage all levels and functions in an organization to maximize overall production efficiency besides tuning up existing processes and equipment by reducing downtimes, mistakes and accidents.
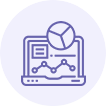
Accountability
A vital part of our Total Productive Maintenance consulting is to train workers to take care of the equipment with which they work. Our TPM training consultants work with your team on preventive maintenance, mistake-proofing equipment, to eliminate product defects and to make maintenance easier.
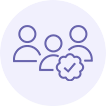
Impact
Combining TPM pillars and tools with our TPM consultants expertise helps organisations reduce breakdowns by 50% and improve OEE by 25%.
Our Client Results
We are global TPM consultants offering TPM consultancy services worldwide in more than 20 countries.
“Integrating TPM with digital capabilities can help companies eliminate losses, maximise equipment efficiency, save more money and ensure higher performance of their operations. We provide expertise and tools to identify improvement opportunities and enhance operational excellence.”
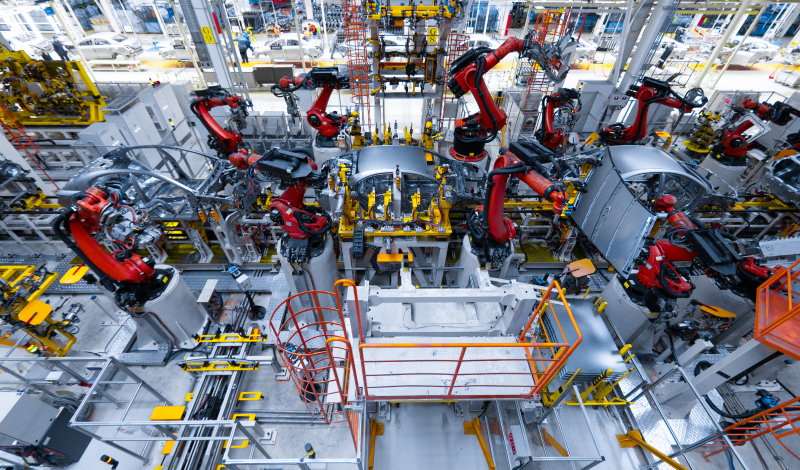
Frequently Asked Questions
Q1. What is TPM?
Answer: TPM is a holistic approach and methodology that is used to achieve perfect production by improving equipment effectiveness, productivity, and minimising losses. It uses comprehensive preventive maintenance strategies to drive the effectiveness of production cycles.
Q2. Why is TPM important for businesses?
Answer: TPM is important for businesses because it improves equipment performance, eliminates wastes, boosts productivity, and creates a culture of continuous improvement. It also gives a sense of ownership to workers by making them responsible for maintenance of equipment.
Q3. What are the main objectives of TPM?
Answer: The main objectives of TPM that every business should aim for are: zero breakdowns, zero accidents and zero defects, leading to productivity maximisation. Apart from the main objectives, TPM implementation also creates a safe work environment and improves employee engagement.
Q4. What are the benefits of Total Productive Maintenance?
Answer: The following are the benefits of Total Productive Maintenance:
- Improved equipment effectiveness
- Reduction in downtime and maintenance
- Improvement in employee productivity and engagement
- Reduction in work-related accidents.
- Safer and cleaner work environment
- Improved and standardised quality.
- Less unplanned equipment maintenance.
- Cost and time savings.
Q5. What is OEE?
Answer: OEE stands for Overall Equipment Effectiveness. It is an effective measure (%) to determine the productivity of a manufacturing equipment in comparison to its full capacity. Most manufacturing businesses want to keep an OEE score between 65% and 85%.
Q6. How to calculate OEE?
Answer: OEE is calculated by a formula: (Availability %) x (Performance %) x (Quality %). Here each component measures a different type of loss in manufacturing process.
Q7.What are the Pillars of TPM?
Answer: There are total 8 pillars of TPM:
- Focused improvement.
- Autonomous Maintenance.
- Quality Maintenance.
- Planned Maintenance.
- Early Management.
- Training and Education.
- Safety, Environment, and Health
- Administrative and Office TPM
Q8. What major losses are reduced by TPM implementation?
Answer: The major losses reduced by successful TPM implementation are:
- Breakdown Loss
- Maintenance Loss
- Startup Loss
- Defects and Reworks
- Performance Loss
- Yield Loss
- Loss of Resources
Q9. How much time does it take to implement TPM?
Answer: The time to implement TPM depends on the project scope and size of the plant. However, an effective and consistent TPM implementation can take anywhere between 3 to 5 years. The primary reason for such a long duration is the training and participation required to be given to operators for resorting and maintaining the equipment.
Q10. What does TPM Training include?
Answer: A TPM training typically includes classroom and workshop floor training on how to leverage TPM pillars and tools. The knowledge of TPM pillars and training empowers workers to maintain and prevent OEE losses of the equipment.