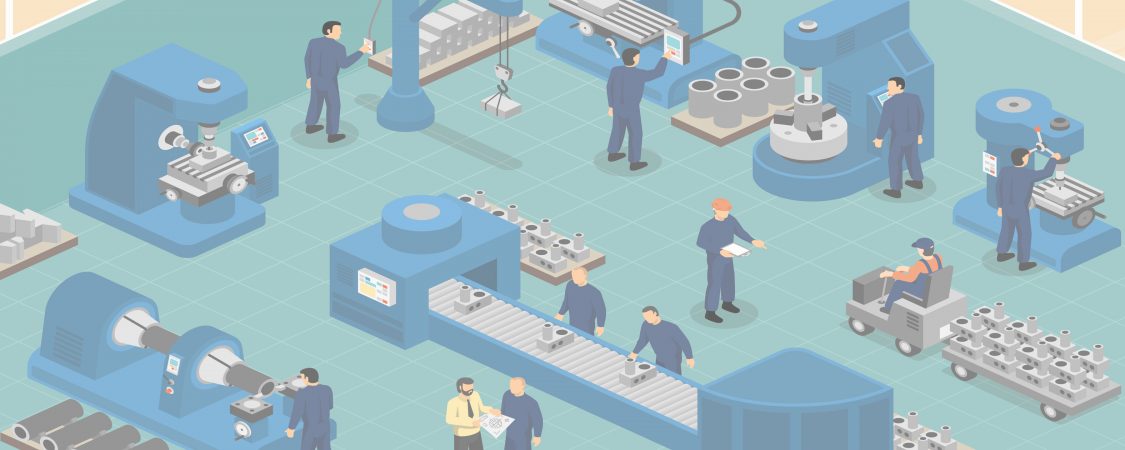
TPM Certification Training
Total Productive Maintenance (TPM) Certification Training will expose you to the latest Preventive Maintenance techniques to help you improve overall equipment effectiveness (OEE) of machines. You will learn how to implement various TPM pillars in an organisation resulting in improved system reliability, decreased costs of replacements, less system downtime and increased safety for machine operators.
Course fee : $500/participant
Date
May 21 – May 29, 2020
Time
6:00 pm – 8:00 pm (Kenya time)
Online Training
Google Meet
16 hours of online training
Interactive sessions with TPM Expert
Access to course content
Case Studies and Assignments
TPM online exam
TPM course completion certificate
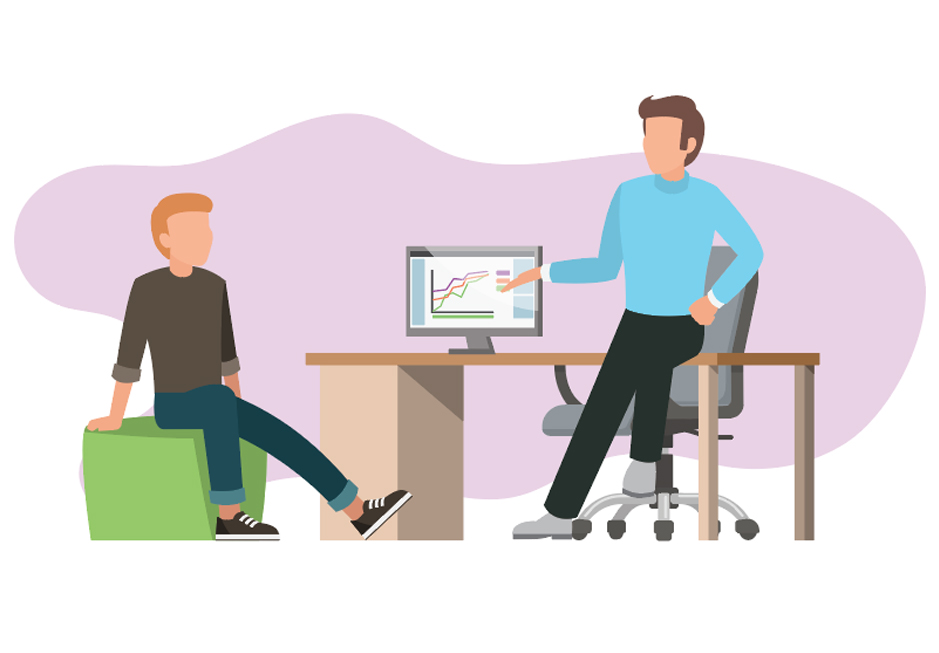
What you’ll learn?
Grasping and practicing the fundamentals of Total Productive Maintenance
How to extend the life cycle of assets using TPM pillars
Identification and steps of reducing OEE losses
Arriving at the root cause of problems to stop them from reoccurring in the future
Using Autonomous Maintenance to increase ownership and responsibility of the operators for their work process
Latest Preventive Maintenance methods to increase reliability and availability of machinery
Deploying Predictive Maintenance to overcome your day-to-day maintenance challenges
Designing solid maintenance plans and schedules for sustainable operational effectiveness
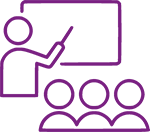
Who is it for?
TPM certification training course is meant for any professional seeking career growth in production, maintenance, operations and engineering department or seeking hands-on experience working with TPM tools and techniques. This training is intended for all who is associated with the production system, from engineers and supervisors to shop floor workers, maintenance personnel and support staff. There is no eligibility criteria for enrolling into TPM certification course.
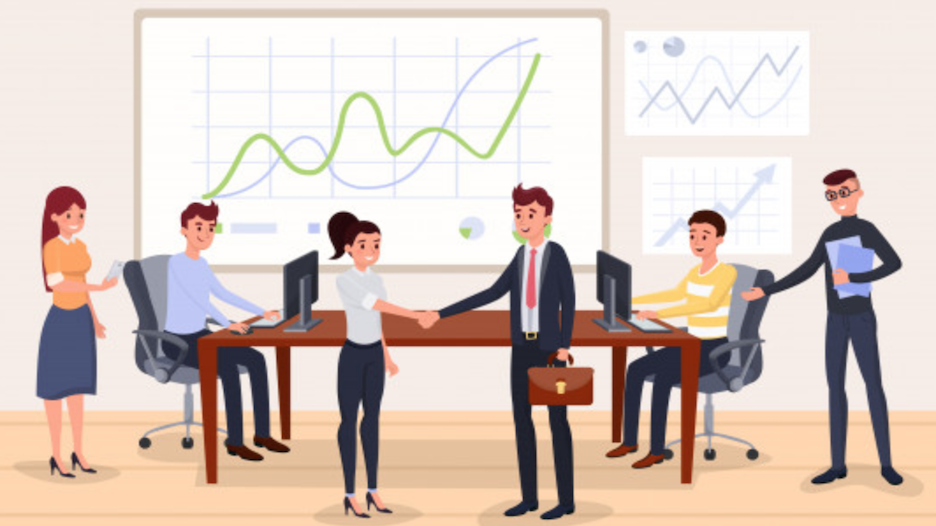
- TPM Introduction
- 8 Pillars of TPM
- Benefits of TPM
- TPM Success Stories
- Summary and Quiz

- Understanding Overall Equipment Effectiveness (OEE)
- Calculating OEE losses
- Understanding Chronic and Sporadic losses
- OEE loss calculation Exercise
- Summary and Quiz
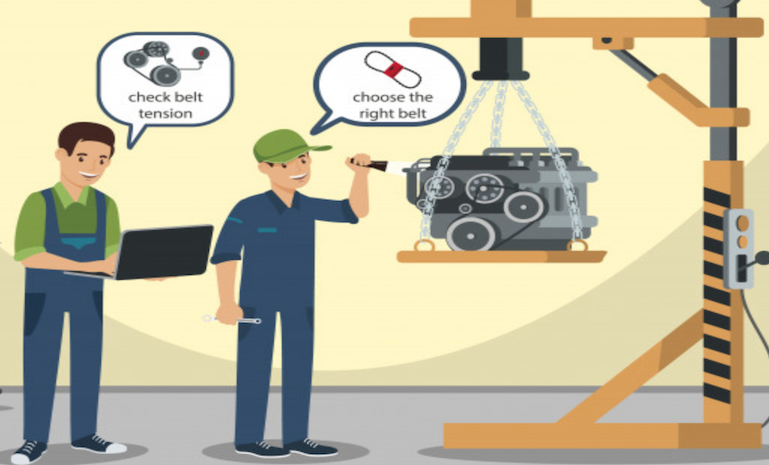
- Understanding concept of Root Cause Analysis
- Steps of Root Cause Analysis – Pareto/Cause-and-Effect Diagram, Gemba validation, and Why Why analysis
- Examples and Case Studies
- Summary and Quiz
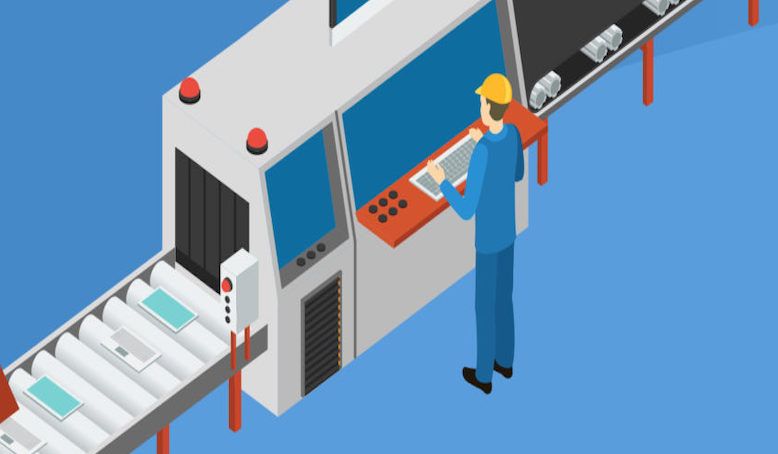
- 7 Steps of Autonomous Maintenance
- Key preparations for successful implementation
- Methodology of Implementing AM Step 1-3
- Case Studies explaining the use and benefits of Autonomous Maintenance

- Support to Autonomous Maintenance
- Evaluation of equipment Failure/ Breakdown status (Equipment Control Ledger and equipment ranking)
- Time based maintenance (TBM)
- Condition based maintenance (CBM)
- Examples and Case Studies
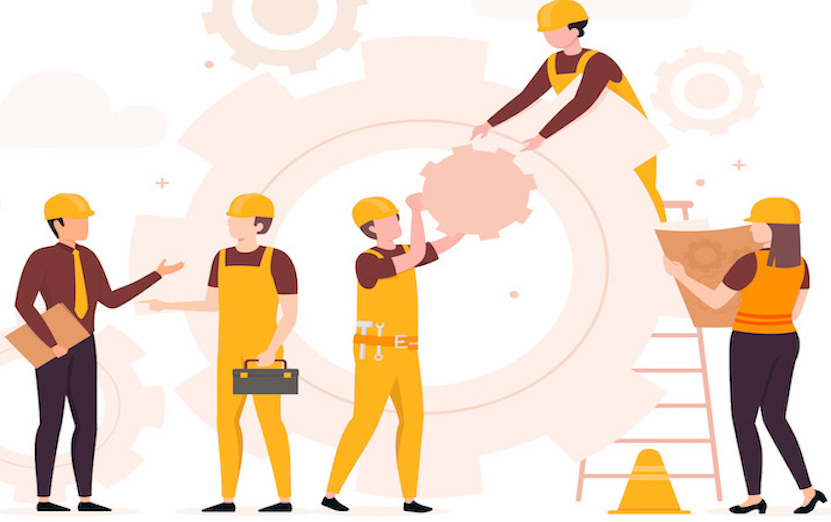
- Understanding concept of Spare Parts Management
- What to keep: Spare Parts Categorization for keeping the right parts
- How much to keep: Calculation of re-order levels and Standard order quantities
- Where and How to keep: Golden rules of Spare Parts storage
- How to Order: Kanban System for Spare Parts Ordering
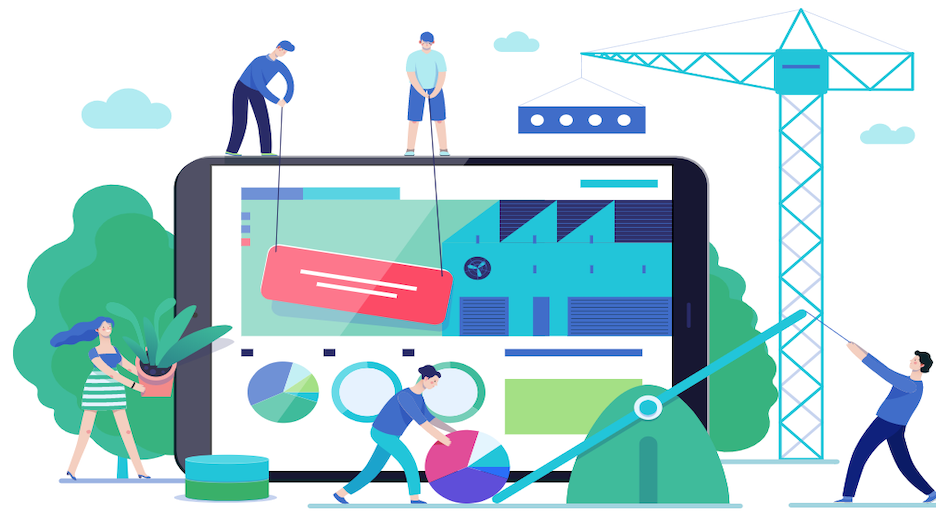
- Predictive Maintenance Introduction
- Predictive Maintenance Techniques including Vibration Analysis, Infrared Thermography, Oil Analysis, Ultrasonic Analysis
- Examples and Case Studies
- Summary and Quiz
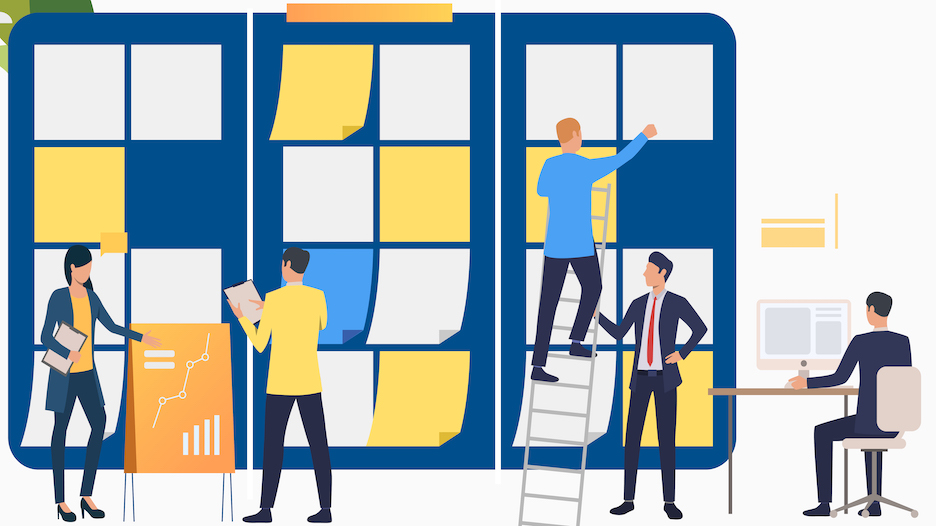
- Improving Maintenance Team Productivity through Planning
- Reducing cost of production using Maintenance Planning & Scheduling
- Creating effective maintenance schedule to prevent breakdowns
- Minimising repeat jobs and reducing MTTR
- Summary and Quiz
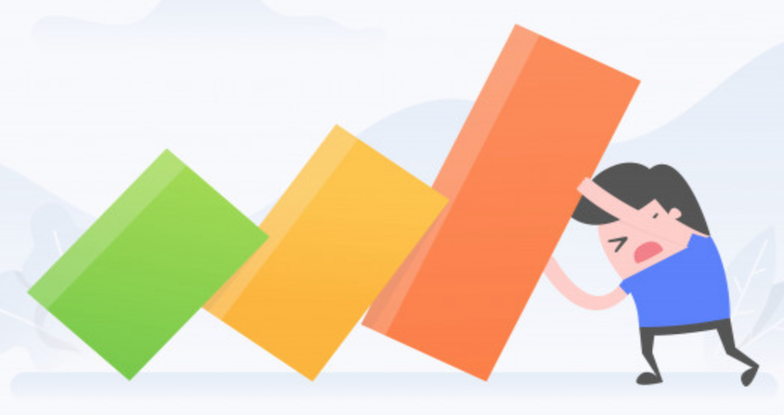
- Understanding concept of FMEA
- Why Failure Mode Analysis?
- Distinguishing failure modes from symptoms
- FMEA process to Identify, analyse and act on failures
- FMEA techniques to Prevent breakdowns and Increase MTBF
- Summary and Quiz
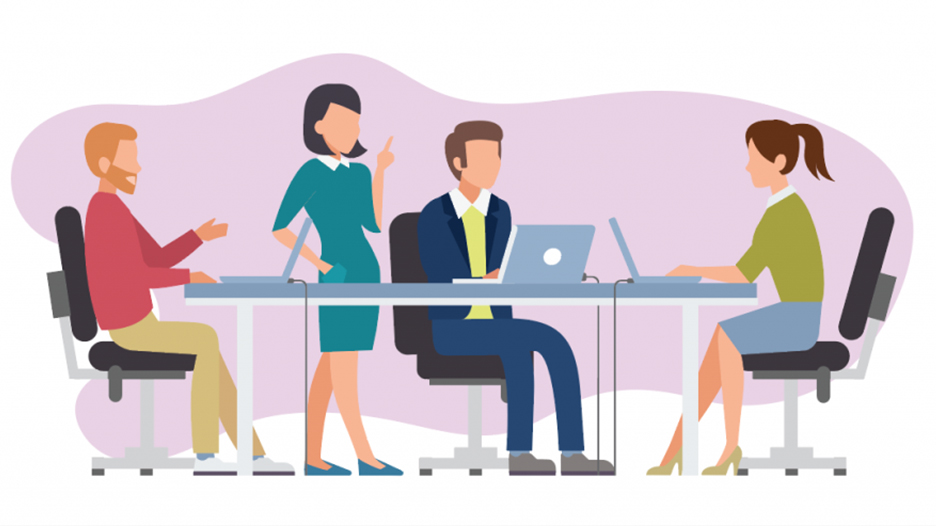
RIBCON Training Advantage
- Combination of educational presentations and case studies
- Productive in-session assignments and participants collaboration to provide actionable learning
- Training by senior consultants with in-depth knowledge and hands-on experience across various industry sectors
Opportunity to get work assignments of TPM implementation
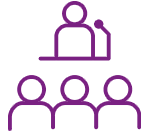
About the Instructors
Our instructors are Kaizen and TPM experts who have worked for more than 100 companies across various industries from past 15 years. Our team has conducted over 250 Kaizen workshops & Trainings on Preventive Maintenance, 5S, Lean Manufacturing, Just-In-Time, Total Productive Maintenance (TPM), Total Quality Management, Total Flow Management (TFM), Daily Work Management, and Hoshin Kanri.
Get TPM Certified
RIBCON conducts an online exam with one project completion at the end of TPM Certification Training program. You need to score 60% to receive a course completion certificate. Enroll today and become TPM expert.