Lean Manufacturing simply means eliminating waste from manufacturing processes including waste of work in progress and finished goods inventories.
What is waste? Waste is any activity that consumes resources but creates no value. Every organisation has lot of scope to improve their current processes by eliminating waste using
Lean manufacturing methods and tools.
Lean manufacturing helps in expanding manufacturing capacity by reducing costs and shortening cycle times. Core idea of Lean manufacturing is to understand what is important to customer and deliver products with no defects in less time with less space, less human
effort, less capital and less material.
So, how to implement Lean?
First step in lean process is to correctly specify the value that the customer seeks in order to cost-effectively solve the customer’s problems.
Once we know what to improve, identify the value stream (including product development, fulfilment and other support processes) and eliminate steps that do not add value.
Designate someone as Value stream manager to align all steps in tight sequence so that product will flow smoothly to customer.
Let the customer pull products through the value stream
In order to seek perfection, repeat this process again to continuously improve quality and eliminate waste
5 Step Lean Process
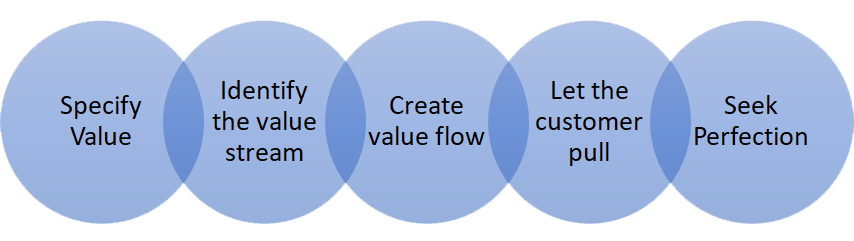
Implementing Lean is not a one-time activity, it’s a journey every organisation should focus on. Here are few key steps to undertake before starting Lean journey:
- Gain top Management “Buy In” and Support
Perform overall company assessment tied to company strategic, operational, and marketing plans
Develop strategic lean deployment plan
Integrate customized training with lean to improve specific skill sets, leverage training resources
Conduct high impact events to create awareness about Lean and its benefits
Hire Lean manufacturing consultants who will help “Transform” organisation’s culture towards Lean processes
Help teams implement various Lean tools and techniques to deliver quality products at significantly lower costs
Key goal is Highest Quality, Lowest Cost, Shortest Lead Time
Let’s look at few key Lean manufacturing tools and techniques that can improve the efficiency, effectiveness, and profitability of manufacturing operations.
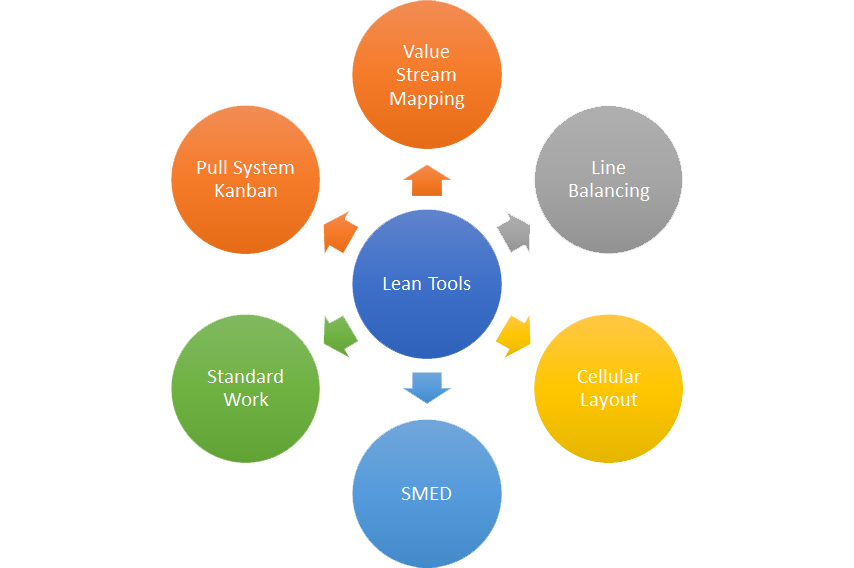
1. Value Stream Mapping
A value stream is all the actions (both value added and non-value added) currently required to bring a product through the main flows essential to every product: i.e. the production flow from raw material into the arms of the customer.
Value stream mapping is a pencil and paper tool that helps you to see and understand the flow of material and information as a produce makes its way through the value stream. It helps you visualize more than just the single-process level, i.e. assembly, welding, etc., in production.
VSM is essential tool for Lean Manufacturing as:
It helps you see more than waste. Mapping helps you see the sources of waste in your value stream.
It helps implement Lean techniques in well-structured manner.
It forms the basis of an implementation plan. Working on Lean tools without VSM is like building a house without a blueprint!
It shows the linkage between the information flow and the material flow. No other tool does this.
It is much more useful than quantitative tools and layout diagrams that produce a tally of non-value-added steps, lead time, distance traveled, the amount of inventory, and so on.
Value stream mapping is a qualitative tool by which you describe in detail how your facility should operate in order to create flow.
2. Line Balancing
Line Balancing is a technique to balance the work load of each process to the customer demand rate (also known as TAKT time). Line balancing requires measurement of cycle time of each process, Calculation of TAKT time and then matching cycle time to TAKT time.
Key steps followed in Line Balancing are:
Measure Cycle Time (how frequently finished unit comes off) and record details of each activity done
Calculate TAKT time (Time available per day/Average Demand per day)
Plot cycle time against TAKT time
Calculate number of operators required
It is much more useful than quantitative tools and layout diagrams that produce a tally of non-value-added steps, lead time, distance traveled, the amount of inventory, and so on.
Re-distribute the work content of cycle time
Line Balancing helps in improvement in manpower productivity, reduction in WIP, skill improvement of workers.
3. Cellular Manufacturing (Flow Production)
Key objective of Lean Manufacturing is to establish Material and information flow at pace of customer requirement. First stage of flow production is creating one-piece flow in current equipment, layout, and operation methods to reveal concealed waste in the factory. This technique is called Cellular manufacturing, where all equipment and processes are placed next to each other. Equipment or operations can be arranged in straight line or in form of U Shape. U shape layout helps improve manpower productivity by minimizing motion waste, thus allowing operators to do multi operations.
Key benefits of implementing Cellular manufacturing are:
WIP reduction by more than 95%
Manpower Productivity improvement by min 25% to more than 100% in some cases
Space reduction by 30%
Quality defects reduction by 30-40%
4. Pull System – Kanban
Pull System is a method to control material flow by replacing only what has been consumed. In Pull system, downstream process sends a signal to an upstream process indicating what it need. The upstream process sends only the material requested. The signal sent to upstream processes is called a Kanban.
Pull system is main tool to reduce & minimize MUDA of Overproduction and inventory. Pull System help reduce costs by allocating only required resources to meet the customer demand and serves as basis of reduction of many other wastes such as waiting, transportation, motion and defects.
5. SMED (Single Minute Exchange of Die)
SMED, being an acronym for Single-Minute Exchange of Die, refers to a theory and techniques for performing setup operations in under ten minutes, , i.e., in a number of minutes expressed in a single digit. Key idea is to minimize time from last good product to next good product by eliminating all wasteful activities, using standard work, parallel work & methods to eliminate adjustments.
Major benefits of SMED system are:
- Reduction of Changeover times thus improvement in Equipment OEE
- Reduction of Batch Sizes
Reduction of Inventories thus allowing high variety small lot production
6. Standard Work
Standard work is key element of lean manufacturing and no improvement can be done without standard work. Standard work can be stated as “Best, Safest and Easiest Way to do a particular task”. Doing standard work helps eliminate waste and thus improve quality, productivity & safety. Standard operations is an effective combination of workers, materials, and machines for making high- quality products cheaply, quickly, and safely.
In order to implement these Lean tools effectively, it’s important to conduct Lean workshops, a five-day Learn by doing workshop at manufacturing facility, with the help of Lean manufacturing consultants. These consultants come with years of direct, front-line experience across wide range of industries. During this workshop, key problems are identified through initial assessment and specific Lean tools are implemented to successfully achieve the project objectives.
Good news is that Lean manufacturing is not just limited to one industry. It has benefited lot of industries across all sectors including:
Automobile & Auto Components
Drugs & Pharmaceuticals
FMCG
Plastics
Food
Printing & Packaging
Sheet & Metal
Textiles
Machine Building
Foundries
Organisations who have successfully implemented Lean Manufacturing are able to serve their customer in half the time with half the hours of human effort, half the investment, half the costs, half the space and minimal inventories. By adopting Lean principles and practices, company can reap many benefits that results in greater profitability:
• Smaller lot sizes
• Increased capacity / throughput
• Higher inventory turns
• More available floor space
• Improved quality
• Reduced inventories
• Reduced delivery time, cycle time, set-up time
• Reduced cost
• Improved employee involvement, morale, and company culture
• Improved customer satisfaction
It is very critical that people involved have buy-in to implement changes & sustain them for greater results. Availing Lean Consulting services from established service providers can help companies plan and strategize implementation, gain employee participation, train employees across the firm on best practices and of course sustain the benefits long-term by formulating suitable processes and procedures, which will be refined continuously as well.