The 5S approach is a simple but powerful method for shopfloor improvement. Progressive shopfloor improvement techniques are vital for companies who want to stay competitive and to achieve world-class excellence. Companies must find new ways to ensure the survival in this competitive environment by adapting to the changing business needs.
5S is a powerful improvement process that gives impressive results. Main challenge of implementing 5S is developing a shopfloor understanding of its key points and tools.
Learn how to put this powerful and proven improvement tool in the hands of your entire workforce. Implementation of five pillars of 5S is the starting point in the development of improvement activities.
The five pillars are defined as:-
1. Sort 2. Set in Order 3. Shine 4. Standardise 5. Sustain
We practice these five pillars in our personal lives without even noticing it. We do keep our things like wastebaskets, towels, clothes etc using Sort and Set in Order.
These 5 pillars are in fact the foundation for achieving zero defects, cost reduction, safety improvements and zero accidents. 5S system sounds simple and basic, but we do forget to realise the importance in the daily work of a workplace.
a neat and clean workplace has higher productivity
- a neat and clean workplace produces fewer defects
- a neat and clean workplace meets deadlines better
- a neat and clean workplace is a much safer place to work
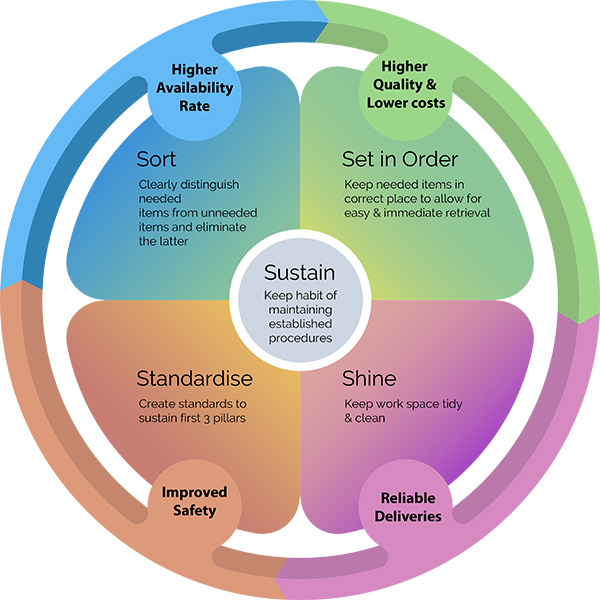
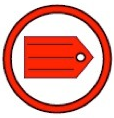
Sort
When in doubt, move it out –red Tag Technique

Set in order
When in doubt, move it out –red Tag Technique
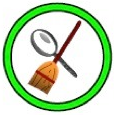
Shine
When in doubt, move it out –red Tag Technique
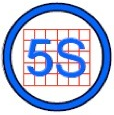
Standardize
When in doubt, move it out –red Tag Technique
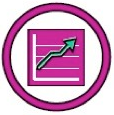
Sustain
When in doubt, move it out –red Tag Technique
Sort means that you remove all items from the workplace that are not needed for current production (or clerical) operations. Implementing this first pillar helps in
- Effective utilization of space, time, money, energy, and other resources
- Reducing problems and annoyances in the work flow
- Improving communication between workers
- Increasing product quality and productivity
It means implementing 1S by tagging all unneeded items with conspicuous “Red Tag”.The most difficult is to differentiate what is needed or what is not or may be needed later. Three key factors that helps determine what is needed or not are:
How useful the item is in our daily workflow?
- If the item isn’t needed it should be disposed of
How frequently the item is needed?
- If it is needed infrequently it can be stored away from the work area
How much quantity of the item is needed at work?
- If it is needed in limited quantity the excess can be disposed of or stored away from the work area
a neat and clean workplace has higher productivity
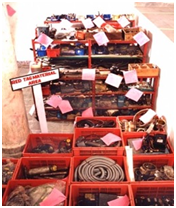
Systematic Arrangement means that you arrange needed items so that they are easy to use and label them so that anyone can find them and put them away.Key steps of systematic arrangement are what to store, how much to store, where to store and how to store.
- In order todecide on appropriate locations, 5S Map is a tool that can be used to evaluate current locations of parts, jigs, tools, equipment, and machinery, and to decide best locations for these items.
The next step is to identify best locations using The Signboard and Painting Strategies that helps to identify, what should go where and in what quantities.
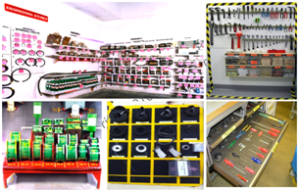
Shine means that we keep everything swept and clean. Key purpose is to keep everything in topcondition to be ready to use as and when needed.In order to implement Shine in your workplace, one should determine:
- Shine targets
- Shine Assignments
- Shine Methods
- Shine Tools and
Implement Shine
5S Schedules and the FiveMinute Shine are the common tools used in the implementation of Shine.
Once cleaning becomes a part of our process, it’s important tostart incorporating systematic inspection procedures into our Shine procedures. This turns “cleaning” into “cleaning/inspection.”Cleaning/Inspection Checklists and Checklists of Needed Maintenance Activities helps in inspection process.
Standardise helps to maintain the first three pillars-Sort, Set in Order, and Shine.
Why standardise?
To be able to do & sustain 3S (Sorting, Systematic arrangement and Shining Cleaning) work in the best known way
To ensure that quantity & quality of work is consistent
To provide a basis for improvement
To provide a basis for daily management/ supervision
To provide a basis for training new employees
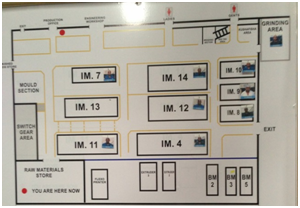
Here are some of the Standards to be created as a part of 5S implementation:
What items should be kept in the areas & what items should not be kept
Red Tagging and Red Tag disposal Standards
Systematic Arrangement Standards
Standards on How much to Store
- Standards on Where to Store
Standards on How to Store
- Labeling& Signboard Standards
- Floor Marking Standards
- Shadow Board Standards
Cleaning Schedule
Cleaning Standards
Sustain means maintain 4S- Sort, Systematic arrangement, Shine and Standardize.
Maintain the gains from other 5S activities and improve. Workplace with commitment to sustain 5S conditions enjoy high productivity and high quality. It includes:
- Determine 5S Level of Achievement
- Perform routine checks
- Analyse results of routine checks
- Measure progress and plan for continuous improvement
- Conduct 5S Training to everyone in Production using 5S Training plan
- Conduct Regular Audits on 5S by setting 5S Audit calendar
To help sustain 5S activities in your company, it’s important to conduct 5S campaigns using mostcommon tools – 5S Slogans, 5S Posters, 5S Photo Exhibits and Storyboards, 5S Newsletters, 5S Pocket Manuals, 5S Department Tours, and 5S Months.
Implementation of 5S sounds simple but any company introducing these five pillars is likely to encounter resistance.
- What’s so great about it?
Are we not keeping it clean?
We already do Sorting and Systematic Arrangement
We did 5S years ago
We’re too busy for 5S activities
- It gives you an opportunity to provide input regarding how your workplace should be organized and laid out and how your work should be done
- It makes your workplace more pleasant to work in
It makes your job more satisfying
It helps remove many obstacles and frustrations in your work
It helps to know what you are expected to do, and when and where you are expected to do it.
It makes it easier to communicate with everyone you work with
Zero Changeovers leading to product diversification
Zero Defects improving Quality
Zero Waste resulting to Lower Costs
Zero Delays helps in Reliable Deliveries &increasing customer satisfaction
Zero Injuriescreating Safe environment
Zero Breakdowns for Better Equipment Availability
Zero Complaints bringing Greater Confidence and Trust