Medical Device manufacturing involves lot of manual work, thus faces challenges in manpower productivity. Various Lean Kaizen techniques can be used to improve the productivity. A leading medical devices (Rapid tests) manufacturer was facing following problems and approached RIB Consulting for help.
- Low Manpower productivity
- High Overtime hours
- Wasted time after each part production
- Lead time of 2 Days
- High number of defects produced
Our team conducted 4 Day Rapid Improvement – Kaizen Workshop to improve the Manpower productivity. First Day of Kaizen workshop was spent on Assessment of current state using cycle time & motion study. Time & Motion study was performed by breaking down each activity into micro activities & recording time taken to finish them. Observations related to the wasted time / activities were also taken during the study. Time & motion study can be conducted by a stopwatch or videography. Videography is best method for time & motion study.
Following issues were observed from time & motion study:
- Disconnected flow of material
- High WIP
- Wastage due to Transportation
- High Rejection
- Wastage due to Manpower Waiting
- High Overtime Hrs
- No tracking of hourly performance
- Functional batch layout and unbalanced operations
Once time & motion study was completed, Next step was to prepare current line balancing chart based on Cycle Time TAKT Time analysis. TAKT is german word, which means beat or pace. in Lean lingo, meaning of TAKT time is Customer demand rate. Following is Formula for TAKT time calculation
TAKT Time = Time available per day / Customer Demand per day
Next step is to use ECRS (Eliminate, Combine, Rearrange & Reduce) techniques to minimise / eliminate wasteful activities and balance the work load as per TAKT time. During Line Balancing, We must make sure that each activity must be finished and balanced in the multiple of the TAKT Time. i.e., if the Time taken for a certain activity is 2 time the TAKT Time, that means 2 operators have to perform the same activity in parallel.
By performing Line Balancing calculations, it was evident that Time required to produce parts can be reduced significantly & Number of manpower required can also be significantly reduced.
Day 2 of Kaizen Workshop was spent in training the shop floor team and conducting trial as per line balancing analysis. A cross functional team was formed & training the team was conducted on the following topics:
- Preparing Mindset for implementation of Kaizen
- Basics of Kaizen
- Value chain
- Wastes and its types
- PDCA
- Flow Production
- Cellular unit
- Line Balancing
After training, new flow production layout was setup for the first trial.After 1 hr of trial, we achieved just above break even productivity as compared to functional batch production method. Establishing a new processes, takes some time before people get used to the new method. Most of time, there will be tendency to go back to old method, but trial must be conducted for a longer duration and continuous improvements must be made to achieve the set targets of productivity improvement
On Day 3 of the workshop, trial was continued and competition was created with old method of working in parallel. This day was divided into 4 hour of Batch Production in the first half & 4 hours of Flow production in the second half. In batch production, the number of people allocated from first process to final process had to be changed over the hours based on judgement. There was a lot of time and effort wasted in moving the WIP from one room to the other. 3 rooms were occupied for the same.In flow production, the entire setup was done in half a room. With the new setup team was getting used to the system and gradually the output increased each hour.
Results: At end of Day 3, Flow productivity results were 36% more than that achieved by all the best effort put into batch production.
Day 4: Synchronisation & Setting up performance metrics: This day was spent on adapting to the speed of the line. Where if a certain activity is lagging due to any reason & an operator is idle, that operator will perform the lagging activity to balance the line. Also a verbal Andon system was created, where if any issue an operator is facing, then the supervisor will rush to the station to help, solve the problem or stop the line.Performance metrics were setup to monitor the hourly progress & reason for non compliance was recorded. As a result, Day 3 performance increased a lot and we have achieved 43% improvement in productivity as compared to batch production.
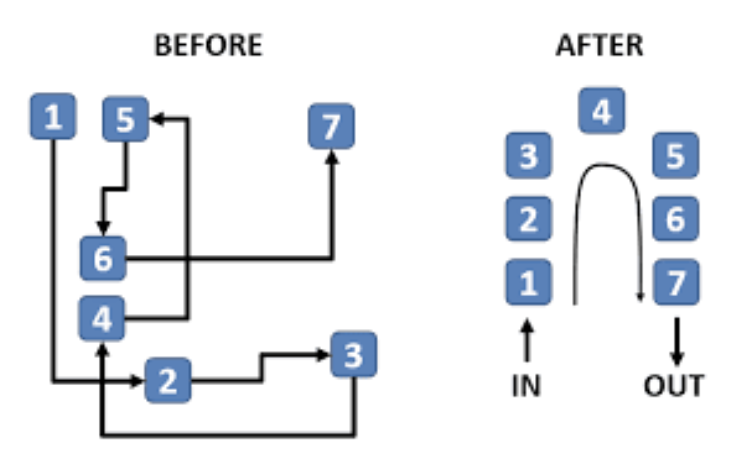
Manpower productivity improvement, Layout improvement
Summary & Learnings: By assembling products using batch production, a lot of manpower is utilised to achieve maximum output at each unit, but it doesn’t result in maximum output as because a lot of time is additionally wasted in batch production due to high WIP, transportation of WIP. Rejection is created to meet the target and the rejection cannot be tracked back to its origin in most of the cases.
By switching to a single piece flow production with a cellular layout, WIP can be reduced to a maximum of One Piece, Rejection even if created can be immediately identified at the origin & rectified. Line is completely balanced & hence no manpower is waiting. Overtime hours due to low productivity is completely nullified. Believe it or not. This step alone increases your productivity by up to 50%
Major Challenges you will face implementing the change:
Initial resistance from the people: As many of the people are used to the old system, adapting to the new system is hard for everyone. Hence training employees on the benefits and aligning the team for improvements is very important. After which you can also put forward a competition where you will inform the team to give their best effort in giving the maximum productivity possible. Record it, benchmark it. Note – Only count the final product which is a good piece as Output. Then, setup the new system. Let the team get used to it for a day. Next day record the output given out by the team. You will be surprised that you have squashed batch production Output & Productivity.
Lead time dropped from 2 days to 1 hr.
Good Luck with your Lean Kaizen Journey!